Ajrakh is a resist block-printing technique native to Ajrakhpur, in Bhuj, Gujarat, historically connecting to the Indus Valley Civilization. Since the beginning of time, Ajrakh was generally done only on cotton fabric as it was able to bring out the hues of the Ajrakh shades amazingly. The fabric is created through traditional vegetable dyes by using natural and organic substances like indigo, madder, harde powder, pomegranate seeds, and others to dye the fabric. Ajrakh's intricate motifs and patterns are achieved through one of the most sophisticated block printing techniques. According to the widely accepted myth among local practitioners, Ajrakh means "keep it now." It goes through 21 complex steps and can take up to 2 weeks. The cloth has a distinctive quality due to using natural dyes in Ajrakh printing. It causes the fabric's pores to enlarge during the summer, which facilitates airflow. During winters, the pores of the fabric close, producing warmth. It makes sense that Ajrakh is appropriate for wearing throughout the year.
Fabric
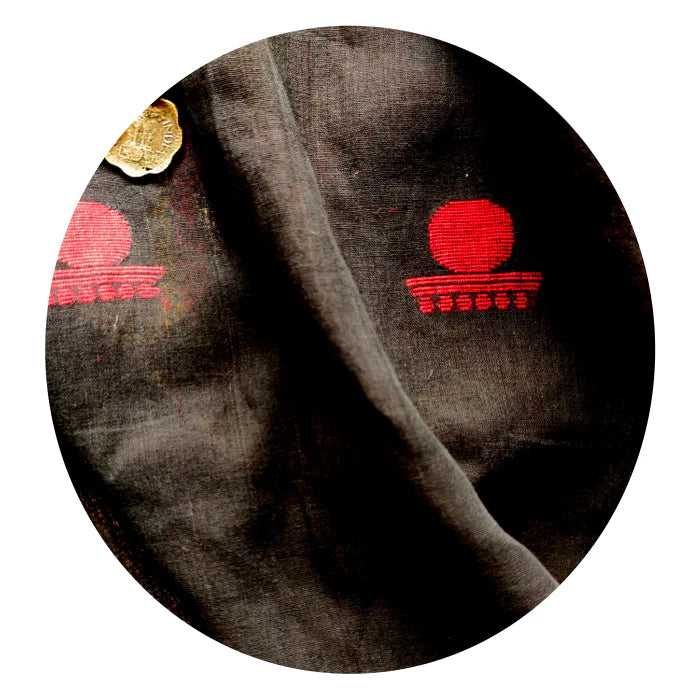
JAMDANI
Jamdani is a discontinuous weft technique of weaving. Jamdani, whether figured or flowery, is a cotton woven fabric. The weavers are incredibly skilled and work efficiently on a handloom to create the fabric. The motifs are inlaid into the fabric when the weaver adds denser thread to fine warp threads by Hand. This handloom weaving technique to achieve the motifs is labor-intensive and time-consuming. Jamdani is believed to be a fusion of the ancient cloth-making techniques of Bengal. The weave is indigenous to Bangladesh. The name 'Jamdani' is of Persian origin and comes from the word "jam," meaning flower, and "dani," meaning vase. According to legends, jamdani patterns mostly feature geometric, botanical, and floral designs that date back thousands of years. Only aristocratic and royal families could afford such luxury because of the exemplary meticulous methodology needed. This is an art of textile weaving popularly known as Dhakai Jamdani or simply Dhakai. The intricateness of the motifs is what displays its beauty and uniqueness. We at Prathaa have been in touch with our loom experts from the villages who have helped to develop this exclusive fabric and exquisite Motifs on the fabric.
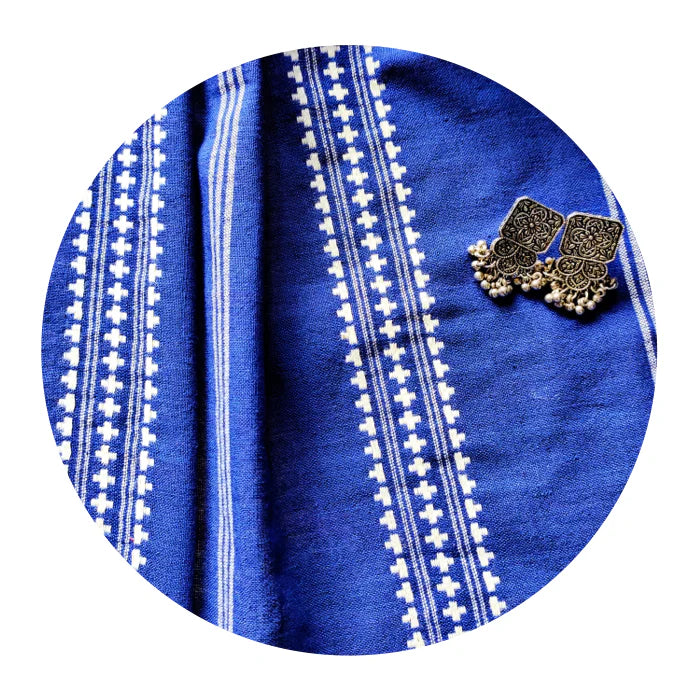
KOTPAD
Kotpad fabrics are woven in the small town of Orissa, Kotpad, by local tribes. The weave is done in hand-spun two-ply cotton yarn. The most significant characteristic of these textile items is their use of organic dyes such as Madder, Indigo, and turmeric. Processing the color and dying the threads in different hues takes roughly 15 to 30 days. Black and maroon are the two primary colors extracted. The fabrics are quite pleasant to wear in the summer and the winter. The motifs are inspired by nature, which includes birds, fishes, and rivers.
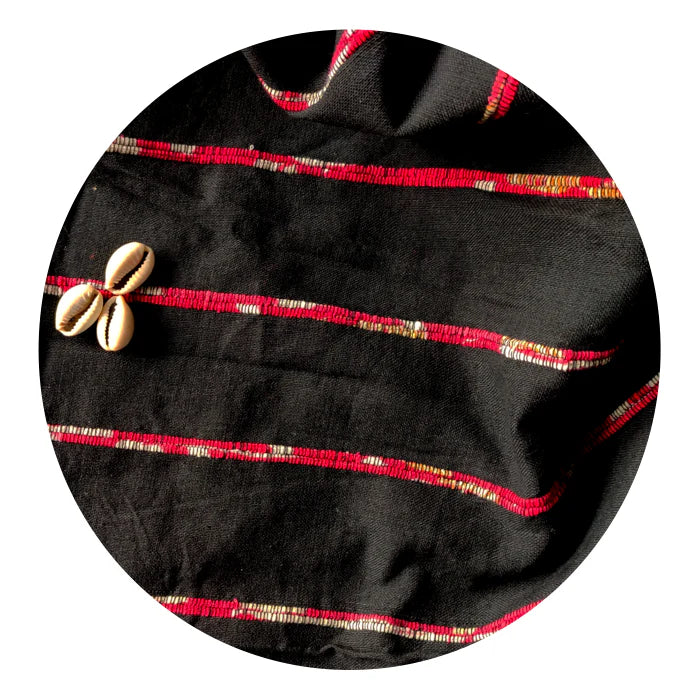
KHESH
The handloom Khesh weave has been very close to our hearts building our sustainability story stronger.The exploration and understanding started when the team visited West Bengal's Birbhum district. The weavers there collect cotton saree, and the women patiently tear the sari into multiple long strips.The thin strips are then incorporated into new fabric. The weaver sits intently on his Hand Loom machine, twisting and adding the thin strips of the sarees to new warp threads to create the unique and up-cycled Khesh weave. It is up to the weaver to match the warp with the weft and create designs. The fabric develops stripes that can sometimes differ in color from meter to meter. The "beautiful irregularity" is precisely its uniqueness.
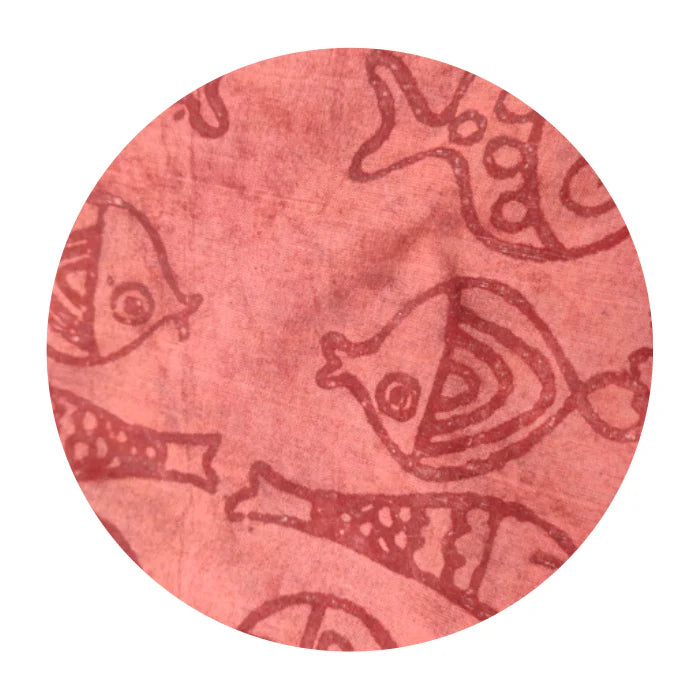
BATIK
Batik is a technique of Hand block printing achieved through resist dyeing. The Gujarati Khatri community was previously recognized as the creators of batik printing. Over time, batik-making practices spread to other Gujarati communities and cultures and eventually to other parts of India. However, it was kept as the métier of aristocratic women because of its delicate hand-painted designs with floral and bird motifs, regarded as symbols of refinement and cultivation. Indigo, brown, and white were frequently utilized in traditional Indian batiks as a tribute to the three Hindu gods, Vishnu, Brahma, and Shiva. The patterns and designs are created with a resist dye from hot wax and plant resins. Batik is usually done in cotton fabric. The fabric goes through many stages of washing, soaking, and dyeing. The shielded patterns are then scrapped off to produce a different color. The process is repeated as many times as the number of colors desired.
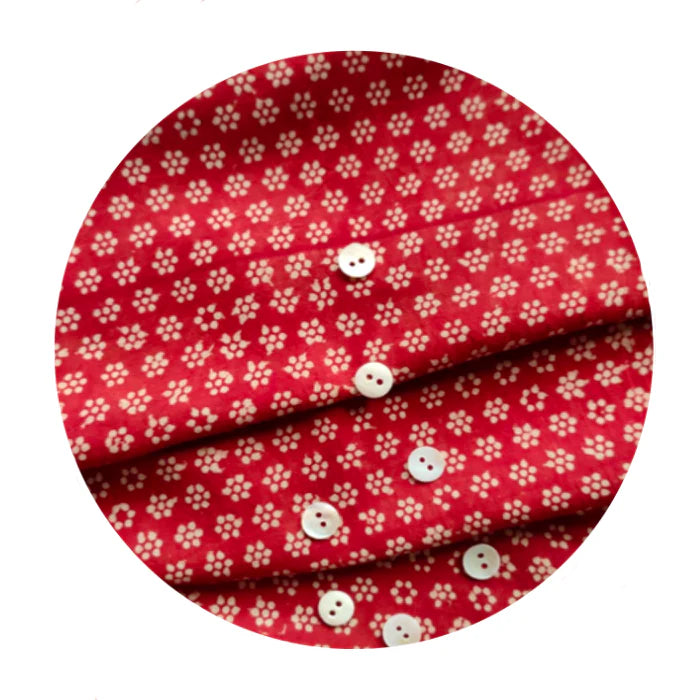
BAGRU
Bagru is a village in Rajasthan where Bagru printing is practiced by Chippa's. The Chippa's have indigenous methods of preparing the cloth and printing the fabrics; a process passed down from generation to generation going back at least 300 years. The mud resists, dyed, and mordant prints of Bagru catered to the folk, trading, agricultural, and artisan communities that comprised the local population. A true Bagru can be distinguished by the sheen given to the finished cloth by the waters of the Sanjara River and a robust color palette of indigo, black, red, green, pink, and orange derived from natural sources. They follow both direct and resist dyeing techniques. Dipping blocks into color and stamping them with a thump of the Hand to ensure a strong print on the fabric is done daily in the village of Bagru. Wildflowers, buds, leaves, and geometric patterns inspire the motifs.
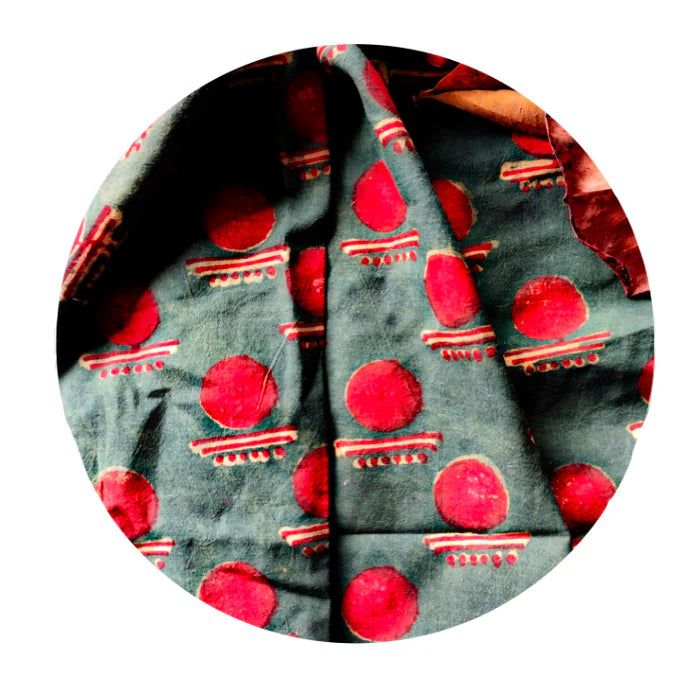
DABU
Dabu is a mud-resist block printing craft that means "to press," derived from the word "Dabanna.". The method of Dabu Printing starts with the preparation of mud resist; clay is made ready by finely sieving it. Calcium hydroxide (Chuna in Hindi), naturally pounded wheat chaff (Beedan in Hindi), and gum (gound in Hindi) are the main ingredients to make the mud resistant. It is a 100-year-old technique that includes 15-22 processes, 25-40 pairs of hands, at least 65 hours spread over six days, and a lot of sand. The artisans of Chaubundi of Kaldera, Rajasthan, efficiently and effectively created this. Once this long-drawn process was understood, it was in sheer awe of the craftsmanship that Prathaa committed to the Dabu form of hand block printing for their emotionally precious signature Bindi collection, the most awaited collection of the year. This time-consuming and labor-intensive process started with the block creation in the Bindi motif, deciding on the size, proportion, and many other minor details. After the formation of the block, they are dipped in oil to prevent them from cracking in the process. The handloom cotton fabrics made from two-ply yarns are cut into 6 meters each and soaked for 2-4 days to ensure better absorption of color. The fabric is then scoured and dried in the sandy soil. Printing begins with alum, followed by a few days of drying in the sun. This printed fabric is washed in running water and simmered in large copper vessels to hold the color. The fabric is again dried in the sun on dried sandy soil. Fabric is now sorted for mud resist and applied to parts of the fabric. It is dried in the sun, followed by dyeing and drying again in the sun. The final product is ready after printing, mud resist, and dyeing. Animal figurines, peacocks, mangos, leaves, and sunflowers are examples of typical nature-inspired themes. There are also wavy lines, dots, and different geometric shapes that are often used. We have created a variety of designs in this Dabu hand-block printed fabric.
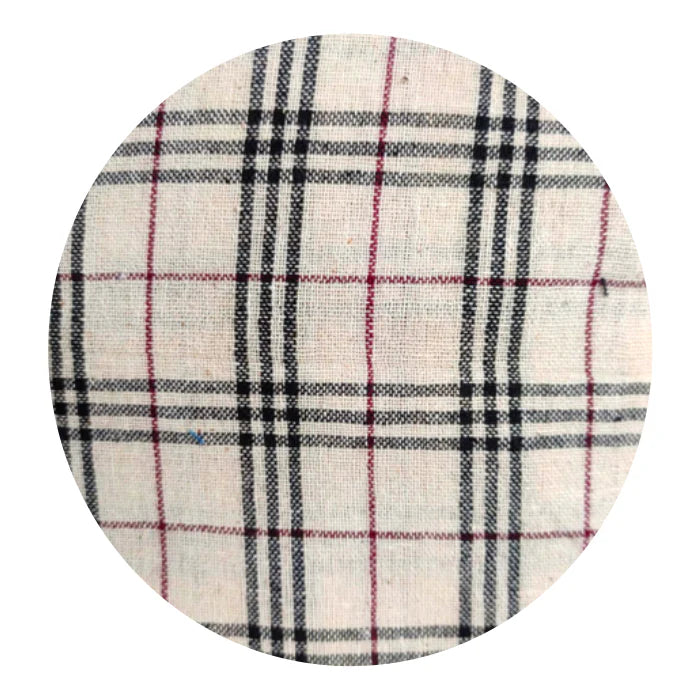
MALKHA
Malkha was named to evoke the heyday of mulmul. Malkha's mission has been to present an evolved alternative to the industrial model of making cotton, eliminating unnecessary steps in the journey from plant to cloth to preserve the earth and the intrinsic properties of cotton rather than please the behemoth machines. The Malkha model of producing handloom cotton revives the local nature, vibrancy, and diversity of the cotton-making process and native cotton species. It seeks to restore handloom cotton to its pre-colonial days of glory. Most significantly, it aims to restore dignity and livelihood, and ultimately financial and functional independence, to each producer in the cotton-making chain. As we stubbornly do adhere to eco-friendly fashion. And in doing so, we embrace not just the vibrancy and brilliance of natural dyes, we welcome the fickleness of nature and the challenge of restoring dying art - the making of natural dyes and the elaborate preparation of cotton that is required for bright, permanent, washable colors. What stands out in this fabric is the vibrancy of the colors and the way it drapes and swings. This tremendous response to Malkha reflects people's intuitive appreciation for its unique qualities – the swing, the drape, and the ability to breathe, absorb, and hold color. Each step in the Malkha process - spinning, weaving, dyeing, and printing - plays a significant role in imparting these qualities to the fabric. Handling the delicate cotton fibers gently and avoiding the force and violence of conventional processing retains the springiness of the live fibers into the cloth.
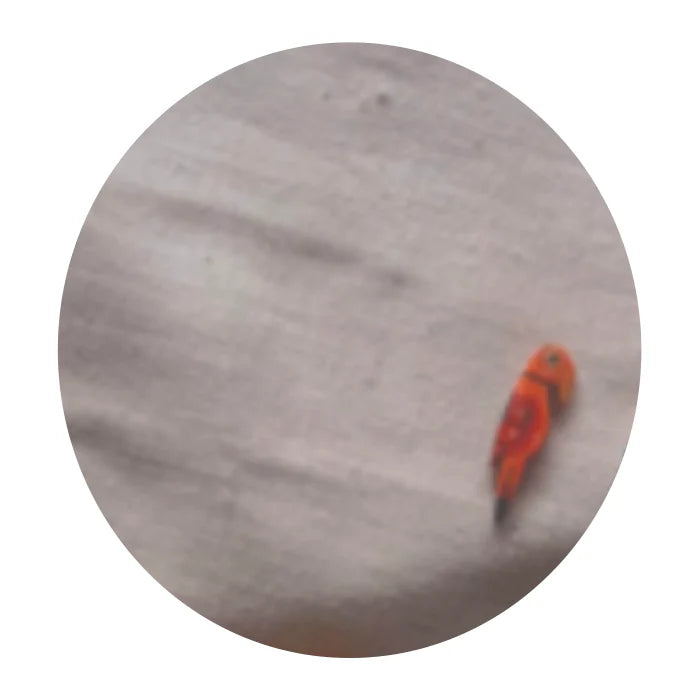
KALA COTTON
Kala Cotton is one of the few genetically pure cotton species remaining in India and one of the only pure, old-world kinds of cotton to be cultivated on a large scale today. Kala cotton is indigenous to Kutch and, by default, organic, as the farmers do not use pesticides or synthetic fertilizers. It is a pure rain-fed crop with a high tolerance for disease and pests, requiring minimal investment. It is both resilient and resurgent in the face of stressful land conditions.